Unlocking Success: Casting Aluminum Made Easy
Unlocking Success: Casting Aluminum Made Easy
Blog Article
Light Weight Aluminum Casting Solutions Revealed: Vital Insights and Tips
Exploring the world of light weight aluminum spreading solutions can introduce a world of intricate procedures and nuanced factors to consider that are vital for effective outcomes. As we venture into the world of aluminum spreading solutions, prepare to reveal the key components that can form the trajectory of your projects and raise your understanding of this complex craft.
The Essentials of Light Weight Aluminum Spreading
What fundamental processes are involved in light weight aluminum casting that create the foundation of this extensively utilized production method? Aluminum casting is a flexible and cost-efficient method made use of in numerous industries to create facility and complex steel components.
After solidification, the mold is gotten rid of, and the casting undertakes completing procedures such as warmth machining, surface area, and treatment covering to satisfy the required specifications. Comprehending these essential processes is vital for achieving top quality light weight aluminum castings with mechanical properties and specific dimensions.
Various Casting Techniques Explained
Discovering the different techniques employed in light weight aluminum casting offers useful insights right into the varied approaches utilized to accomplish specific and elaborate steel components. One common technique is sand spreading, where a mold is created making use of compressed sand around a pattern of the preferred component. This technique is affordable and versatile, ideal for both basic and intricate shapes. One more method, die spreading, includes infusing liquified light weight aluminum right into a steel mold and mildew under high pressure. Pass away casting makes it possible for high precision and repeatability, making it perfect for mass manufacturing of small to medium-sized parts. For more elaborate layouts, financial investment spreading is often preferred. This approach utilizes wax patterns that are thawed away, leaving a tooth cavity for the molten aluminum to fill. Investment spreading yields exact details and smooth finishes, making it preferred in markets like aerospace and vehicle. Each spreading technique has its one-of-a-kind benefits and is chosen based upon variables such as volume, price, and intricacy factors to consider.
Factors to Consider When Picking a copyright
When picking a light weight aluminum spreading solution copyright, evaluating their experience and know-how is critical for making sure quality and reliability in the production process. The supplier's experience in the area indicates their familiarity with various spreading strategies, prospective difficulties, and finest techniques. It is vital to ask about the kinds of jobs they have actually worked on in the past, ensuring they straighten with the complexity and specs of your very own project.
Furthermore, take into consideration the copyright's reputation within the market. Search for testimonials, endorsements, and study that demonstrate their ability to deliver premium aluminum spreadings consistently. A trustworthy copyright will certainly frequently have qualifications or associations with market organizations, showcasing their commitment to excellence and adherence to industry criteria.
Additionally, assess the provider's capabilities in terms of personalization, volume demands, and job timelines. Ensure that they can fit your specific needs and have the flexibility to range manufacturing as called for. Efficient communication and openness pertaining to costs, preparation, and quality assurance processes are likewise important factors to consider when choosing an aluminum spreading service company.
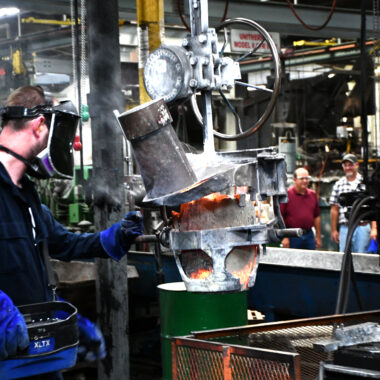
Common Challenges and Solutions
Navigating through the intricacies of aluminum spreading procedures usually provides suppliers with a collection of obstacles that require cutting-edge solutions to make certain my explanation performance and high quality in production. One typical challenge dealt with in light weight aluminum casting is the formation of flaws such as porosity, shrinkage, or additions due to inappropriate mold and mildew design or insufficient steel quality.
One more obstacle hinges on accomplishing precise dimensional accuracy, especially for complex geometries. Variants in cooling down rates, mold and mildew expansion, and product properties can bring about inconsistencies from the designated dimensions. Carrying out sophisticated modern technologies like computer-aided layout (CAD) and computer mathematical control (CNC) machining can boost accuracy and uniformity in light weight aluminum spreading. Additionally, keeping check these guys out correct control over the melting and putting procedures is important to avoid concerns like overheating or irregular distribution of the molten steel - casting aluminum. By buying automation and real-time monitoring systems, suppliers can improve process control and minimize variations, eventually improving the general quality of aluminum cast items.
Tips for Optimizing Your Casting Projects
To boost the efficiency and top quality of your aluminum casting projects, carrying out calculated optimization techniques is necessary. One vital suggestion for maximizing your spreading tasks is to thoroughly develop eviction system. By making sure that the gating system is well-designed and effectively placed, you can improve the flow of molten light weight aluminum and minimize the opportunities of defects in the final spreading. Furthermore, using computer system simulations can assist in analyzing the flow and forecasting of metal throughout the spreading process, allowing for modifications to be made prior to real production begins.
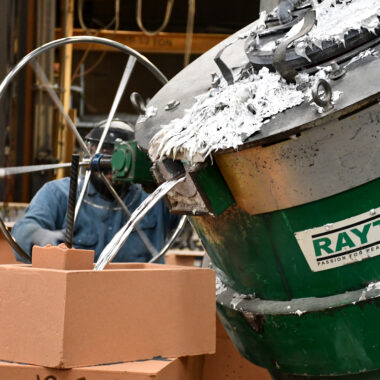
Conclusion
Finally, comprehending the fundamentals of more tips here aluminum casting, different spreading methods, factors to consider when choosing a provider, common obstacles and services, and tips for optimizing spreading tasks are vital for successful results. By sticking to these insights and carrying out best services, practices and people can make certain efficient and efficient light weight aluminum casting solutions that satisfy their details demands and demands.
Recognizing these basic processes is necessary for accomplishing premium light weight aluminum castings with accurate dimensions and mechanical properties.
When choosing an aluminum spreading solution company, reviewing their experience and competence is important for making certain quality and dependability in the production process. Efficient communication and transparency concerning expenses, lead times, and quality control procedures are also critical variables to think about when picking a light weight aluminum casting solution provider.
Browsing through the intricacies of aluminum spreading processes frequently offers producers with a collection of challenges that require cutting-edge options to ensure efficiency and high quality in manufacturing. One typical difficulty dealt with in light weight aluminum casting is the formation of defects such as porosity, shrinking, or inclusions due to inappropriate mold and mildew style or insufficient steel high quality.
Report this page